A Continuous-review Inventory Model With Disruptions at Both Supplier and Retailer
Abstruse
This written report develops a mathematical model to mitigate disruptions in a three-stage (i.due east., supplier, manufacturer, retailer) supply chain network subject field to a natural disaster like COVID-xix pandemic. This optimization model aims to manage supply concatenation disruptions for a pandemic situation where disruptions can occur to both the supplier and the retailer. This study proposes an inventory policy using the renewal advantage theory for maximizing profit for the manufacturer under report. Tested using two heuristics algorithms, namely the genetic algorithm (GA) and blueprint search (PS), the proposed inventory-based disruption take a chance mitigation model provides the manufacturer with an optimum decision to maximize profits in a product cycle. A sensitivity analysis was offered to ensure the applicability of the model in practical settings. Results reveal that the PS algorithm performed meliorate for such model than a heuristic method like GA. The ordering quantity and reordering bespeak were besides lower in PS than GA. Overall, information technology was axiomatic that PS is more than suited for this trouble. Supply chain managers need to employ appropriate inventory policies to deal with several uncertain conditions, for case, uncertainties arising due to the COVID-19 pandemic. This model can help managers establish and redesign an inventory policy to maximize the profit past considering probable disruptions in the supply chain network.
Introduction
Today, every organization in a supply chain experiences disruptions from manmade and natural disasters. For example, the recent novel coronavirus (SARS-CoV-2) as disruption risk is creating complexity in supply concatenation operations since November 2019 (Lopes de Sousa Jabbour et al. 2020). This pandemic outbreak destroys the whole supply concatenation activities past making restrictions in air transportation facilities, border closure, unavailability of raw fabric supply, and entire shutdown of manufacturing activities (Paul and Chowdhury 2020a; Chowdhury et al. 2020; Paul and Chowdhury 2020b; Rowan and Galanakis 2020). As well, the recent estimated data confirmed that the recent pandemic outbreak is a rare case of supply chain disruption that is impacting the global economy dramatically (Majumdar et al. 2020; Karmaker et al. 2020;Taqi et al. 2020). For example, the United nations Conference on Merchandise and Development (UNCTAD) mentioned that the global income will be a shortfall of USD 2 trillion due to the COVID-19 pandemic (UNCTAD Report 2020). Another report conducted by the Earth Merchandise Organization (WTO) confirmed that world merchandise will turn down between 13 and 32% in the year 2020 (WTO 2020). Therefore, to reduce the bear upon of disruptions caused by such a disaster, it is essential to develop a model to manage supply concatenation disruptions (Chang et al. 2015).
Accordingly, this written report develops an inventory system for mitigating such disruptions in a supply chain. A manufacturer with one supplier and one retailer is considered. Information technology is assumed that the supplier and retailer are unavailable for a random period due to disruptions acquired by disaster (say COVID-nineteen, for instance). Also, the reliability of the manufacturer (the ability of a production procedure to produce good-quality products) and the reliability of the supplier (the ability of a supplier to consistently supply adept-quality raw material at the required time) are considered to address defective units produced in the said supply concatenation system (Abdi et al. 2019).
Motivation
An uninterrupted supply chain network is critical to the success of firms in this competitive era of business. Withal, the supply chain network is frequently disrupted due to unavoidable natural (east.k., coronavirus) or manmade disasters (Coelho et al. 2017; Karampour et al. 2020). To ensure the continuity of the supply of products, a manufacturer needs to consider supply chain disruptions caused by a disaster like COVID-xix that may accept place at the supplier and/or the retailer's end. Near of the previous studies considered disruptions at the supplier (e.m., Konstantaras et al. 2019; Paul et al. 2018) or retailer's end (eastward.g., Paul et al. 2018; Sarkar et al. 2017). This study expands such studies by integrating disruptions at the supplier and the retailer'due south end of a supply chain considering the contempo COVID-19 pandemic. In existent-world settings, decision-makers as well need to consider the defective units produced across the supply chain as those defective units hamper the ability of a supply chain to meet client demand (Mehranfar et al. 2019; Nezhadroshan et al. 2020). Therefore, there is a need to include such an of import issue to aid supply concatenation managers in their controlling for supply chain disruption management.
Related works and contributions
Research on supply chain disruption risks gained a lot of attraction in recent years (Govindan et al. 2020; Ivanov 2020; Jabbarzadeh et al. 2018; Al Masud et al. 2014; Pal et al. 2014; Paul et al. 2017; Revilla and Saenz 2017; Sawik 2019; Shokrani et al. 2020; Yoon et al. 2020). The risks resulting from disruptions can be segregated into two categories, risk arising from the mismatch between demand and supply and adventure arising from disruptions in routine activities (Kleindorfer and Saad 2009; Schmitt and Singh 2012). Generally, disruptions tin can be explained as unanticipated incidents that incapacitate the supply chain network of a company (Fathollahi-Fard et al. 2018; Hajiaghaei-Keshteli and Fathollahi Fard 2019; Fathollahi-Fard et al. 2020a; Fathollahi-Fard et al. 2020b; Fathollahi-Fard et al. 2020c; Fathollahi-Fard et al. 2020d). Disruptions in routine activities of a supply chain tin can be caused by either natural events (e.k., hurricane Cindy during 2017 in the United states) or intentional acts (ships attacked by the Somalian pirates, cargo theft, sanctions imposed by the The states government on Islamic republic of iran and other different countries) or accidents (2015 Tianjin explosion in Cathay) or pandemics (the COVID-19 outbreak in Communist china and other countries). These disruptions can drastically hamper the supply concatenation performance too as tin incur huge losses in terms of productivity loss, revenue loss, and harm to the brand'south reputation (Tian et al. 2019a, b). Over the last few years, supply chain disruption direction has become a meaning interest of inquiry (Ambulkar et al. 2015; Amelkin and Vohra 2019; Ivanov et al. 2016; Pavlov et al. 2018; Sawik 2019; Islam et al. 2020).
At present, to survive and to be profitable, a manufacturer needs to ensure the continuous circulation of its products (Tumpa et al. 2019; Kumar et al. 2020; Mehrbakhsh and Ghezavati 2020). Thus, the disruption at the supplier's end as well as the disruption at the retailer's end can consequence in a heavy penalty for the manufacturer in terms of losing customers and reputation, which ultimately results in losing marketplace share. Interestingly, information technology is shown from the recent pandemic situation that both disruptions occurred in the supply concatenation. Also, from the observation of recent literature, we can meet that near of the studies considered disruptions but at i finish. Researchers like Ahmed et al. (2017), J. Chen et al. (2012), Hishamuddin et al. (2012), Konstantaras et al. (2019), Paul et al. (2018), and Snyder et al. (2016) discussed models because disruptions but at the supplier'due south terminate. On the other manus, disruptions only at the retailer's finish were considered in the models past Baghalian et al. (2013), Paul et al. (2018), Sarkar et al. (2017), and Rahman et al. (2018).
The reliability of the production procedure is some other essential factor that can touch the capability of a manufacturer to satisfy client demand (Sarkar 2012; Nujoom et al. 2018; Ilyas et al. 2020). Konstantaras et al. (2019) developed an economic order quantity (EOQ) model where the supplier'south reliability follows an independent Bernoulli process and allows dorsum-social club to fulfill demand. Analyzing the reliability of the procedure for a production inventory model, some literature considered the need as a fuzzy set and incorporated opportunity cost with non-repairable defective productions (Chang 2004; Chen and Chang 2008). Furthermore, nosotros observed that many models considered imperfect production procedure with reliability-dependent production flow and unit of measurement production cost (Tripathy et al. 2011; Al Masud et al. 2014). For an in-depth investigation of the existing literature, we have reviewed the current literature also to clarify the novelty of the study. In the recent study, we have observed that lack of studies has focused on the COVID-19 pandemic to manage the disruption in the supply chain. The findings of the contempo studies are reflected in Table 1.
This study recognizes that for a manufacturer, disruption at the supplier and the retailer's end and the reliability of its product are of high significance in the time of the recent pandemic. Also, the reliability of the supplier is an important factor in addressing demand. This inquiry develops a model for recovering disruptions for a manufacturer's supply chain comprising a unmarried supplier and a single retailer motivated from the recent COVID-xix pandemic situation. We also consider that the supplier's capacity follows an exponential distribution. Also, due to the COVID-19 pandemic, the supplier and the retailer both tin can get disrupted and may non be available during the time cycles. Also, the reliability of the supplier and the manufacturer is considered. In this report, the average turn a profit per wheel is formulated every bit the objective function. This study contributes to supply concatenation disruption risk management literature in several ways. Outset, nosotros include the disruption risk at the supplier and the retailer's finish forth with the reliability of the supplier and the manufacturer'due south product system motivated past the COVID-xix pandemic situation. Second, nosotros consider randomness in the capacities of the supplier and the retailer to tackle disruptions take a chance associated with the level of inventory of existent-word supply chains. Because randomness in capacities is of import equally they influence many supply concatenation decisions.
The residue of this paper is bundled equally follows: "Problem description" presents the problem description followed by the model conception in "Disruption risk mitigation model." Numerical investigations are illustrated in "Numerical investigations." "Sensitivity analysis" offers a sensitivity assay. "Managerial and practical implications" presents the managerial insights of the model. "Conclusions and recommendations for future research" concludes this paper.
Problem description
In this study, we consider a manufacturer who has a single supplier and a unmarried retailer. The supplier and the retailer can get disrupted due to various reasons, due east.g., for the recent COVID-19 pandemic. This disruption is considered to happen at random times. Too, both the supplier and retailer tin can remain unavailable for a random length of time. The available land is denoted equally an ON state and the unavailable country is denoted as an OFF state. As well, we considered the supplier to have a random chapters; as a result, in that location volition be a disparity in his/her capacity to supply the corporeality ordered. For the supplier, the reliability is also considered. The reliability of the manufacturer is also considered in the inventory building process. The reliability of the manufacturing process is also considered for the depreciation cost. The manufacturer needs an inventory model because these facts and too formalizes an ordering policy that will maximize his average profit to avoid the impact of the COVID-19 pandemic. The model allows the manufacturer to back-social club in example of not meeting the demand. The following are some assumptions made for this model:
-
A single type of production is manufactured by the manufacturer.
-
One raw material is used to produce one final product.
-
Production lot size is equal to the ordering lot size.
-
A lower markup than acceptable products is considered for faulty products.
-
Property cost is directly related to process reliability.
-
The ON and OFF states of both the supplier and retailer are unknown to the manufacturer in accelerate. Such an availability and unavailability of the supplier and retailer are obvious in a situation similar the COVID-19 pandemic run a risk. Due to the lockdown of areas and isolation of people, these 2 supply chain agents are not always available to execute the promised supply chain functions.
-
Lengths of availability and unavailability for the supplier and retailer are exponential random variables where the need generation follows the Poisson process.
-
Manufacturer can lodge when both the supplier and retailer are available.
-
The lead time for commitment is zero.
-
Capacity of the supplier follows an exponential distribution.
Using these assumptions and modifying the work of Parlar and Perry (1995), the disruption risk mitigation model is formulated in the next section.
Disruption risk mitigation model
The notations used for the disruption adventure mitigation model are given in Appendix A. The model developed here consists of one supplier and 1 retailer. In this model, at random times, the supplier and retailer can exist available and unavailable. The availability is indicated by ON and unavailability is indicated by OFF. The length of elapsing of the ON and OFF periods is considered to be exponentially distributed for both the supplier and the retailer. The parameter for the length of ON and OFF periods for the supplier and the retailer is given below:
Parameter for length of ON period | Parameter for length of OFF period | |
Supplier | λ | μ |
Retailer | α | β |
Renewal reward theory is the part of probability theory that is used to generalize the Poisson process for random interarrival times (Ross 1995). In a renewal reward process, each interarrival time is associated with a random variable that is ordinarily thought of as the reward connected with the interarrival time. Concept from renewal reward process is used to identify the regenerative cycle and thereby develop boilerplate objective functions for this model.
In this model, depending on the ON and OFF states of the supplier and retailer, at that place can be iv unlike states. These states are shown beneath:
-
State 0: Supplier – ON, Retailer – ON
-
Country 1: Supplier – ON, Retailer – OFF
-
State 2: Supplier – OFF, Retailer – ON
-
State three: Supplier – OFF, Retailer – OFF
In state 0, we can meet that both the supplier and retailer are available. In states 1 and ii, either the supplier or the retailer is available. Also, in land three, both of them are unavailable at the same fourth dimension. In this model, we considered that guild can be placed in state 0 as both the supplier and the retailer are bachelor and it can be reached to the end customers. In state 0, the reordering quantity is r. In the remaining iii states, either the supplier or the retailer remains unavailable. In those states, the product cannot reach the customers. As a upshot, there is only one society quantity (q 0), which will be at country 0. Equally the state of both the supplier and retailer can alter, the transient probabilities are considered. The transient probabilities are stated every bit X ij (t) = probability (being in country j at time t starting at state i at time 0), i, j = 0, 1, ii, 3. At present, the trouble resembles four-state continuous-fourth dimension Markov chain (CTMC). Based on the assumptions made earlier, the supplier has a random capacity and it follows an exponential distribution with parameter 휃 having distribution function F(x) where F(x) = 1-east −θx . This ways whenever he/she received an order of q units, the amount he/she delivered volition be either q or less than that (whichever applicative) and depends on the values of its distribution part, density function, and the corporeality ordered. From now on, the corporeality delivered by the supplier is going to be denoted every bit E(q) throughout the following parts.
In this model, the manufacturer has a single supplier from whom it replenishes its inventory and keeps production running from the raw material inventory. When the supplier gets disrupted for a random menstruation, the manufacturer faces random disruptions in supply. On the other hand, the retailer tin can remain unavailable for random times. The ordering policy for the manufacturer is that it will lodge q 0 units after reaching the reordering point, with the land existence 0. When either the supplier or the retailer is not available, he has to await for the time when both of them become available once more. Upon receiving the supply from the supplier, the inventory level becomes East (q i ) + r; i = 0, i, ii.
And so, the objective function for profit is
$$ \mathrm{AP}\left(q0,r,{n}_s,{n}_m\right)=\frac{X_{00}}{T_{00}}=\frac{Eastward\left[\mathrm{turn a profit}\ \mathrm{per}\ \mathrm{bicycle}\right]}{E\left[\mathrm{length}\ \mathrm{per}\ \mathrm{wheel}\right]} $$
(1)
The profit can be calculated as the difference between the revenue generated and the cost incurred in a wheel. Subsequently computing the acquirement generated per cycle R 00, cost per cycle C 00, and the cycle length T 00 (see Eqs. (24)–(34) in Appendix B), the final objective role can be written as below:
$$ \mathrm{AP}\left(q,r,{northward}_s,{northward}_m\right)=\frac{X_{00}}{T_{00}}=\frac{R_{00}-{C}_{00}}{T_{00}}=\frac{P\times {m}_1\times E(q)\times {northward}_m+P\times {m}_2\times East(q)\times \left(1-{n}_m\right)-{X}_{00}{A}_0-X{\sigma}_1-{X}_{02}{\sigma}_2-{X}_{03}\left(\overline{C}+{\rho}_1{\sigma}_1+{\rho}_2{\sigma}_2\right)}{\frac{E(q)}{\gamma }+X{T}_{10}+{X}_{02}{T}_{20}+{10}_{03}\left(\overline{T}+{\chi}_1{\rho}_1+{\chi}_2{\rho}_2\right)} $$
(2)
Equation (ii), the final objective function, is a nonlinear and unconstrained office. Here, we have four decision variables: quantity ordered, reliability of the supplier, reliability of the manufacturer, and reordering points. A decision-maker (the manufacturer here) seeks to maximize the objective function by optimizing the conclusion variables. To optimize the objective function, this report uses the genetic algorithm (GA) and pattern search (PS) technique due to the following advantages:
-
GA is an advanced optimization method that can search parallel from a population of points, whereas traditional optimization models can search from a single bespeak (Fu et al. 2019).
-
GA follows probabilistic choice rules, whereas traditional models follow deterministic rules.
-
GA can operate on the Chromosome, which is an encoded version of the potential solution parameter, rather than the parameters themselves.
-
GA is a powerful optimization tool that can manage fitness scores without considering auxiliary information (Sahebjamnia et al. 2018).
-
PS is some other dynamic numerical optimization methods that tin can perform without a gradient. Therefore, it tin can be used on functions that are not continuous or differentiable (Malik and Sarkar 2020).
-
PS optimization method can perform better to search for solutions in a multidimensional analysis space of possibilities environment with the lowest error value (Paul et al. 2015).
Numerical investigations
Our model builds the inventory system of a manufacturer considering Poisson need with incertitude of the supplier and retailer along with the random chapters of the supplier and the reliability of the supplier. We consider quantity ordered, reliability of the supplier, reliability of the manufacturer, and reordering points as the decision variables. The values of the different parameters used in the model are given in Table ii. Nosotros also used the cost of involvement and depreciation, in the course used by Cheng (1989), as we have shown in the model evolution section. Here, we used a = 1000, b = 0.8, and c = 0.75.
Here, we are because a modified (Q, r, n southward , due north thousand ) policy formed in this model for a manufacturer with one retailer and one supplier. The goal is to maximize the value of the objective role by optimizing the conclusion variables.
Nosotros used the GA and the PS algorithms to solve the model. In the next department, we are going to discuss the results.
Results
For the GA algorithm, stall generation (G) has been varied to have a better assessment of the effect. For each number of generations, the algorithm was run fifteen times, and the best value was taken. Now, let the states look at the different relationships betwixt the profit and the decision variables every bit presented in Table iii and Figs. 1 and two.
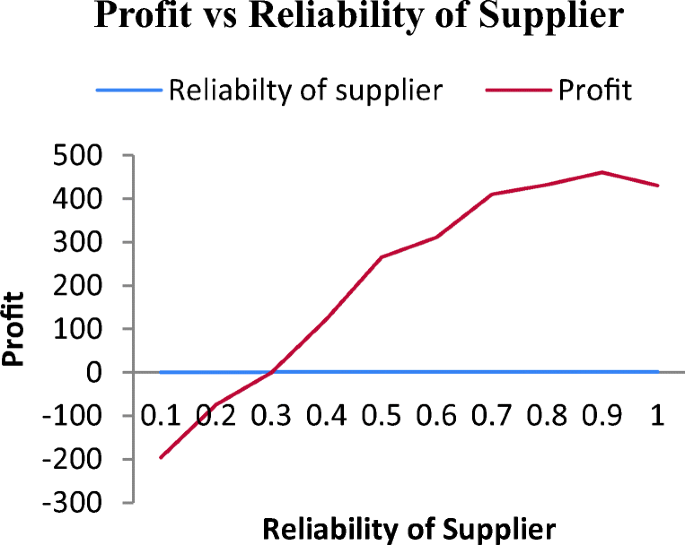
Boilerplate profit vs reliability of the supplier for GA
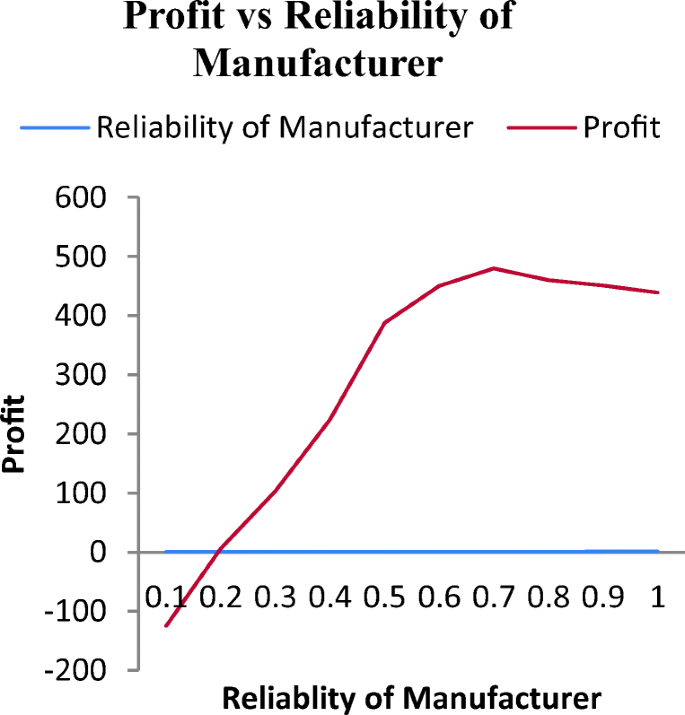
Boilerplate profit vs reliability of the manufacturer for GA
In Fig. 1, equally the reliability of the supplier improves, the boilerplate turn a profit too increases. Nosotros can notice the turn a profit to be negative at lower reliability, which tin exist caused by college property price as well equally high inspection and rejection price. The average profit increased with reliability. Maximization occurs just after crossing the 0.9, and then, the profit shows a decrease again. From Fig. ii, we tin can see that when the reliability of the manufacturer increases, the boilerplate profit likewise increases. Maximization of profit occurs merely when the reliability of the manufacturer crosses the value of 0.7, and then, the turn a profit shows a decrease over again.
From Fig. 3, we can see that with the increase in ordered quantity, the profit increases upwards to a sure ordering quantity nearing 100 units. Initially, for a lower ordering quantity, the ordering price is higher than the belongings cost. Even so, the increase in the holding cost due to increased ordering quantity affects the total profit afterwards that point.
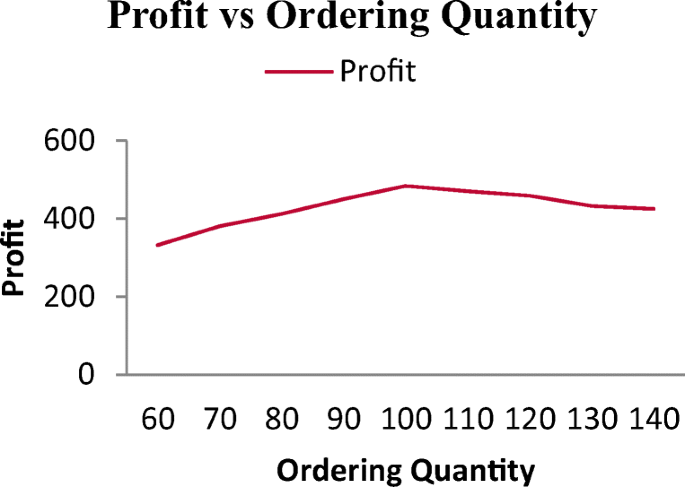
Average turn a profit vs ordering quantity for GA
Figure iv describes the variation in profit concerning the reordering betoken. In the kickoff, the increased reordering bespeak increased the turn a profit up to the optimum betoken. The underlying reason is that a higher reordering point can significantly improve the shortage problem too as the backlog orders. This results in a subtract in their cost, which in turn results in a college turn a profit margin. However, a higher reordering point across the optimal point results in college prophylactic stock. Afterward, the belongings cost increases and rapidly reduces profit.
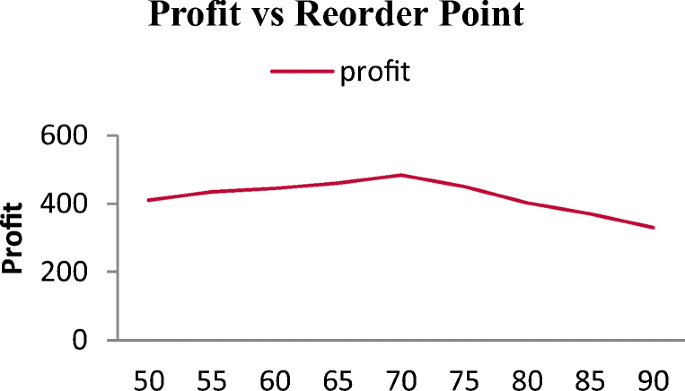
Average profit vs reordering indicate for GA
Nosotros besides used the PS algorithm to optimize the values of the conclusion variable to get the maximum profit in a cycle. In that location are three results summarized in Table 4, which are obtained through the PS algorithm. Maximum number of iterations (1000) has been varied to take a meliorate assessment of the result. From the result, we tin can encounter that the consequence remains almost the same for the change in the iteration number. With the increase in iteration number, the profit increased by a small margin, and after 400 iterations, the result becomes static with insignificant change.
Now, using the pattern search algorithm, nosotros look at the unlike relationships between the turn a profit and the decision variables, presented in graphs. Effigy 5 reveals the almost similar result as we take seen from the GA. The average turn a profit increased with an increase in the supplier's reliability. Initially, when the reliability of the supplier is less than 0.3, the turn a profit is negative. Withal, the profit increases with an increase in reliability. Profit maximization occurs just later crossing the 0.8, and and then, the profit shows a subtract again. Figure half-dozen reveals the influence of the manufacturer'southward reliability on the profit. From the graph, we can meet that when the reliability increases, the boilerplate profit too increases. The gradient is maximum betwixt the ranges of 0.four and 0.5. The profit becomes maximum merely after crossing the 0.7, and then, the turn a profit shows a decrease again. This indicates that trying to achieve a high level of reliability results in more price than actually increasing turn a profit.
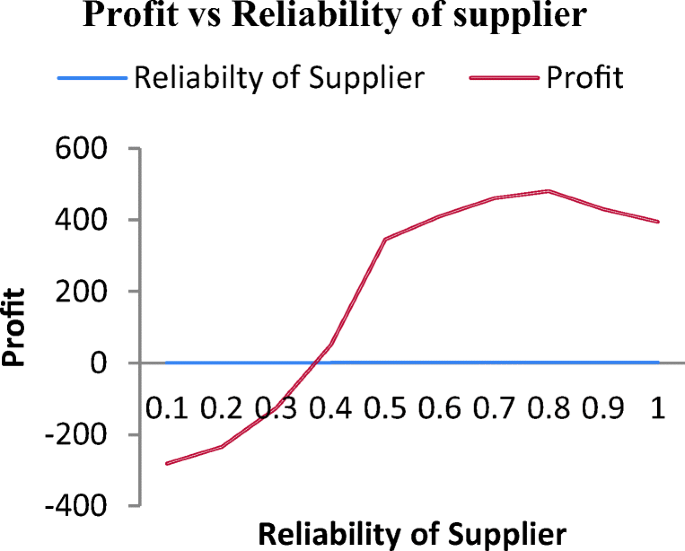
Average profit vs reliability of the supplier for PS
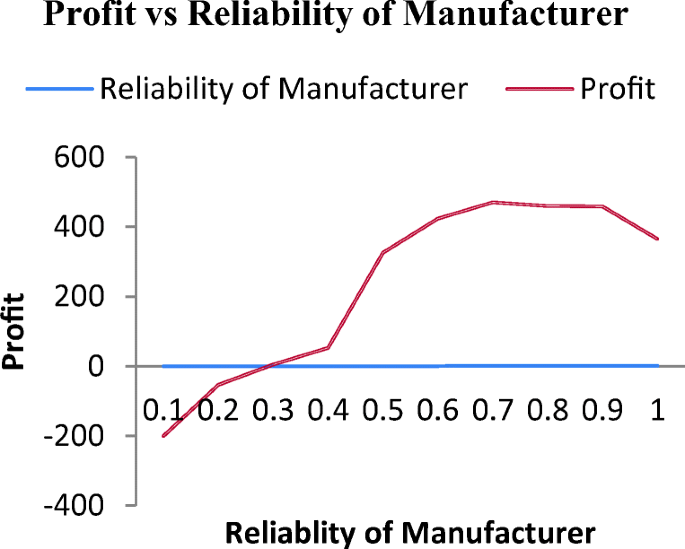
Boilerplate turn a profit vs reliability of the manufacturer for PS
From Fig. 7, we tin observe that the profit increases with the ordering quantity until it reaches the saturation point at the marker effectually xc. This increase in profit is due to the lowering of ordering toll, which is more prominent than the holding cost for small ordering quantity, though increased ordering quantity after the optimum ordering betoken increases the total toll. This is reflected in the profit. Figure eight reveals the variation in turn a profit concerning the reordering betoken. In the beginning, the increased reordering betoken increased the turn a profit up to the optimum point. All the same, the higher reordering point beyond the optimal betoken results in higher holding costs of increased safe stock and apace reduces the profit.
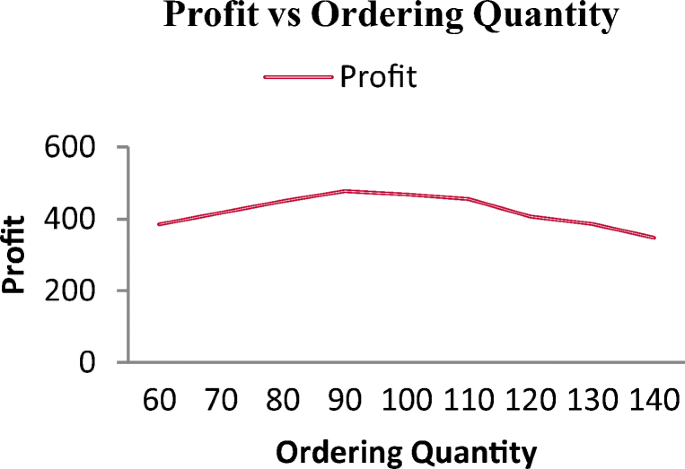
Average profit vs ordering quantity for PS
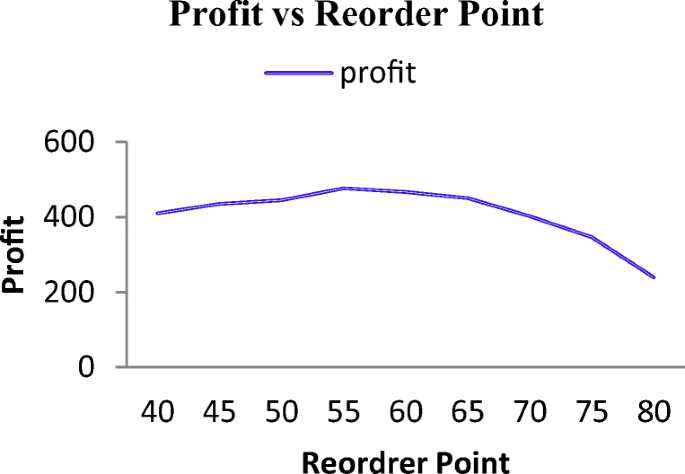
Average profit vs reordering point for PS
We optimized the model using two algorithms – the GA and PS. For the GA, we checked the model by increasing the stall generation at 50 iterations starting from 100. For each generation number, we ran the algorithm 15 times and selected the best among the results. We continued this upwardly to 600 iterations. On the other hand, for the blueprint search, we started with 100 iterations. Then, we increased the iteration by 100 at each step. The optimization finally terminates afterwards 1018 iterations.
From the results, we find that both GA and PS requite almost identical results, but PS produced better results than GA in near cases. The reason may underlie in the working process of these two algorithms. For GA, which is a stochastic search process, sometimes, information technology converges to local optima or even capricious points rather than the global optimum of the problem. In contrast, PS finds a sure search direction, which helps it to perform meliorate than many search-based algorithms.
Sensitivity analysis
To written report the effects of the parameters of the model, a sensitivity analysis is performed with the illustrative example described earlier. In Table 5, the basic value of the parameters as considered in the example is represented in level one. In the following columns, level 2 represents the values at + 20% of the bones level, whereas level 3 represents + 40%. For each of these parameters, we run both the GA and the PS to solve the model. The event from the sensitivity analysis is shown in Table vi.
From the sensitivity assay, we have identified that our most sensitive parameters for this model are h southward , h m , P, thou 1 , and γ. For these parameters, nosotros then checked the variation in profit by increasing them by 10%, xx%, 30%, and forty% and showed them in Table 7.
For h s , sensitivity analysis reveals the fact that when raw cloth belongings cost is increased, both ordering quantity and reordering betoken decrease. It reflects that if the holding toll is high, the material should be ordered in a lower quantity. Besides, to go on the safety stock at minimal, the reordering indicate should be ready at a lower point accordingly.
For h m , it is seen that when the finished material property price is increased, it affects the ordering quantity too as the reordering betoken. They both decrease. The turn a profit level also decreases. For P, which is the purchasing price, increasing it affects the profit past a significantly large margin. It also increases the requirement of the manufacturer's reliability by a large corporeality.
For m ane , an increase in grand ane influences the turn a profit positively past direct increasing the selling price. Even so, increase in chiliad one requires proper market analysis, equally it tin impact the product sales directly. From the analysis, information technology can be said that m 1 is a insufficiently more sensitive parameter equally any increase in m 1 reduces the value of the quantity ordered.
For γ, nosotros constitute that the ordering quantity as well as the reorder quantity is readily influenced by the change in demand charge per unit. Both increase rapidly with the increase in need rate. The demand charge per unit likewise highly influences the average profit value. So, we should be conscientious while irresolute the circumstances that tin affect the turn a profit maximization objective.
Managerial and practical implications
The model developed in this study can help managers to deal with disruptions in the supply chain while maintaining profitability in the context of COVID-nineteen pandemic. The COVID-19 pandemic is creating complexity in the supply chain operations by making unavailability of suppliers. This unavailability of suppliers can create randomness in its capacity and reliability. Therefore, this written report considered randomness in the capacity for the supplier along with its reliability to capture the real-life situations. Also, the reliability of the manufacturing process is introduced, equally it influences the power of the manufacturer to supply with acceptable products to sell in the sudden disruption condition. The managerial implications of the model in the context of COVID-19 are presented below:
-
Supplier reliability and random chapters
Randomness in capacity in the electric current pandemic state of affairs is a mutual occurrence for suppliers in real life. Though it is the responsibility of the supplier to supply the amount ordered, in the pandemic situation, the managers of the manufacturing entity should take into business relationship the randomness of the capacity of the supplier while sourcing. Also, the supplier's reliability is another important concern for supply chain operations. Managers need to accept the reliability of the supplier into account to showtime its effect. This can assist the managers to brand a revised plan for the alleviation of disruption risk of a supply chain caused by the COVID-nineteen pandemic by considering these factors while making decisions.
-
Reliability of the manufacturer
The reliability of the manufacturer plays a vital role in the profitability of the manufacturer. Although the ideal situation dictates for a reliability level of a hundred percent, in real life, due to various reasons like the COVID-19 pandemic, this is not doable. Furthermore, information technology is too seen that in the COVID-19 pandemic, state of affairs increasing the reliability of the manufacturing system is financially prohibitive in proportion with the return on investment. Thus, the optimum reliability of the manufacturing process considering the COVID-xix pandemic to stay profitable in the face of disruption in the supply chain is an important decision factor for supply chain managers.
-
Inventory management policy
Developing efficient inventory direction policies considering the current pandemic COVID-xix state of affairs is crucial for business organisation organizations to satisfy customers and maximize profit. Therefore, supply chain managers need to reduce the cost related to the inventory, like warehousing and ordering cost, and they need to make certain that the production process runs smoothly with sufficient raw textile at hand. Even so, the COVID-xix pandemic state of affairs is creating trouble to manage sufficient raw textile supply. Therefore, this model tin can assistance managers to establish a revised model and make changes to the inventory policy to maximize the profit by guiding their purchasing decision.
Conclusions and recommendations for time to come enquiry
This report offered an inventory model to manage supply chain disruption risks. The model maximizes the profit of the manufacturer as a role of guild quantity, reordering betoken, and manufacturer and supplier reliability. This model indicates the optimum level of reliability required to maintain profitability for a manufacturer. Equally a faulty manufacturing system produces defective products, procedure reliability is a major concern to increase the profit. However, increasing process reliability comes with an added cost of operation, which can reduce the profit margin. In developing countries, smaller manufacturing industries frequently lack whatever rigorous inventory policy to accost any kind of uncertainty in their supply chain. Manufacturing industries, specially where the defective product can be recycled like soap industry and plastic industry, oftentimes ignore their manufacturing process reliability, which can impact their ability to stay assisting when faced with disruption in their supply chain during the COVID-nineteen pandemic. A single product is ofttimes manufactured from a concert of many items. Disruption in the supply of a single particular due to COVID-19 can potentially delay the whole production process, which is now seen in the fix-made garments (RMG) sector. Considering the reliability of the supplier during the purchasing policy can alleviate this problem to a big extent. At that place are also other sources of disruptions like epidemic outbreak, accidents, natural calamities, strikes, trade embargo, and fifty-fifty holiday at the sourcing country. For case, in recent times, we accept seen the sudden catastrophic bear on of COVID-nineteen on the global supply chain. Every bit one of the biggest raw textile suppliers for almost all industries, the closure of China due to the pandemic resulted in the shutdown of product in manufacturing industries globally. This pandemic is impacting the global supply chain terribly by creating uncertainty in supply, manufacturing, and demand. Therefore, this model tin can assistance to address such disruptions from the unavailability of suppliers, which are random practical settings.
Also, in most of the recent studies, it is assumed that the supplier will always be able to supply the amount ordered, which is not the example in real-life scenarios, especially in the COVID-19 situation. This model considered limited capacity for the supplier to make it more realistic. The generation of demand is considered to follow the Poisson process, and the availability and the unavailability period of the supplier equally well equally the retailer are considered to follow an exponential distribution. The objective function of this model is formulated by using concepts from the renewal reward theorem, which is a part of average bike profit. We used the GA and the PS to maximize the function. We got a improve result from PS for this item model. Lastly, we conducted a sensitivity assay to investigate the implication of the parameters and their relationship with the decision variable and influence on the boilerplate turn a profit. In summary, the model considered capacity randomness along with reliability in conjunction with disruption at both the retailer and the supplier due to a disruption like the COVID-19 pandemic to take a amend anticipation of the existent operating atmospheric condition.
In this research, we considered the reliability as a conclusion variable that is non-integer by value and deterministic. In future enquiry, reliability can be considered every bit probabilistic to alter the model. A manufacturer may have multiple suppliers. In this study, only a single supplier was considered for the manufacturer. Therefore, the piece of work can be extended by considering multiple suppliers for the manufacturer because the epidemic outbreak. In this inquiry, zero lead time has been considered, although in reality, there is e'er a finite lead fourth dimension associated with the orders. Hence, lead fourth dimension may be introduced in the model. Furthermore, instead of a continuous-time Markov concatenation (CTMC), a semi-Markov chain tin be used for transient probabilities.
Data availability
In that location is no linked data for this article. Data and materials related to this article are provided in the main manuscript.
References
-
Abdi A, Abdi A, Fathollahi-Fard AM, Hajiaghaei-Keshteli One thousand (2019) A prepare of calibrated metaheuristics to address a closed-loop supply chain network design problem under dubiety. International Periodical of Systems Science: Operations and Logistics:1–18. https://doi.org/10.1080/23302674.2019.1610197
-
Ahmed I, Sultana I, Azeem A (2017) Development of an inventory model for 2 suppliers with random chapters because supply disruption. International Journal of Logistics Systems and Management 26:57. https://doi.org/10.1504/IJLSM.2017.080630
-
Al Masud A, Paul SK, Azeem A (2014) Optimization of a product inventory model with reliability considerations. Int J Logistics Systems and Direction 17(1):22–45
-
Ambulkar S, Blackhurst J, Grawe South (2015) Business firm's resilience to supply concatenation disruptions: scale development and empirical examination. J Oper Manag 33-34:111–122. https://doi.org/ten.1016/j.jom.2014.xi.002
-
Amelkin V, Vohra R (2019) Strategic Formation and Reliability of Supply Chain Networks. http://arxiv.org/abs/1909.08021
-
Baghalian A, Rezapour S, Farahani RZ (2013) Robust supply chain network design with service level against disruptions and demand uncertainties: a real-life case. Eur J Oper Res 227(1):199–215. https://doi.org/10.1016/j.ejor.2012.12.017
-
Chang HC (2004) An awarding of fuzzy sets theory to the EOQ model with imperfect quality items. Comput Oper Res 31(12):2079–2092. https://doi.org/ten.1016/S0305-0548(03)00166-7
-
Chang W, Ellinger AE, Blackhurst J (2015) A contextual approach to supply chain risk mitigation. Int J Logist Manag 26(three):642–656. https://doi.org/10.1108/IJLM-02-2014-0026
-
Chen SH, Chang SM (2008) Optimization of fuzzy production inventory model with unrepairable defective products. Int J Prod Econ 113(2):887–894. https://doi.org/10.1016/j.ijpe.2007.11.004
-
Chen J, Zhao Ten, Zhou Y (2012) A periodic-review inventory organisation with a capacitated fill-in supplier for mitigating supply disruptions. Eur J Oper Res 219(2):312–323. https://doi.org/x.1016/j.ejor.2011.12.031
-
Cheng TCE (1989) An economic product quantity model with flexibility and reliability considerations. Eur J Oper Res 39(2):174–179. https://doi.org/10.1016/0377-2217(89)90190-ii
-
Chowdhury MT, Sarkar A, Paul SK, Moktadir MA (2020) A case written report on strategies to deal with the impacts of COVID-19 pandemic in the nutrient and beverage industry. Oper Manag Res. https://doi.org/x.1007/s12063-020-00166-9
-
Coelho KR, Cherri AC, Baptista EC, Chiappetta Jabbour CJ, Soler EM (2017) Sustainable operations: the cutting stock problem with usable leftovers from a sustainable perspective. J Clean Prod 167:545–552. https://doi.org/10.1016/j.jclepro.2017.08.153
-
Darom NA, Hishamuddin H, Ramli R, Mat Nopiah Z (2018) An inventory model of supply chain disruption recovery with condom stock and carbon emission consideration. J Make clean Prod 197:1011–1021. https://doi.org/10.1016/j.jclepro.2018.06.246
-
El Baz J, Ruel S (2020) Can supply chain risk direction practices mitigate the disruption impacts on supply chains' resilience and robustness? Evidence from an empirical survey in a COVID-xix outbreak era. Int J Prod Econ 107972:107972. https://doi.org/10.1016/j.ijpe.2020.107972
-
Fathollahi-Fard AM, Hajiaghaei-Keshteli M, Mirjalili S (2018) Multi-objective stochastic closed-loop supply concatenation network pattern with social considerations. Applied Soft Computing Periodical 71:505–525. https://doi.org/10.1016/j.asoc.2018.07.025
-
Fathollahi-Fard AM, Ahmadi A, Al-e-Hashem SMJM (2020a) Sustainable airtight-loop supply concatenation network for an integrated water supply and wastewater collection arrangement under uncertainty. J Environ Manag 275:111277. https://doi.org/10.1016/j.jenvman.2020.111277
-
Fathollahi-Fard AM, Ahmadi A, Goodarzian F, Cheikhrouhou N (2020b) A bi-objective habitation healthcare routing and scheduling problem considering patients' satisfaction in a fuzzy environment. Appl Soft Comput J 93:106385. https://doi.org/10.1016/j.asoc.2020.106385
-
Fathollahi-Fard AM, Hajiaghaei-Keshteli Chiliad, Tavakkoli-Moghaddam R (2020c) Crimson deer algorithm (RDA): a new nature-inspired meta-heuristic. Soft Comput 24:14637–14665. https://doi.org/ten.1007/s00500-020-04812-z
-
Fathollahi-Fard AM, Hajiaghaei-Keshteli M, Tian One thousand, Li Z (2020d) An adaptive Lagrangian relaxation-based algorithm for a coordinated h2o supply and wastewater collection network design problem. Inf Sci (Ny) 512:1335–1359. https://doi.org/10.1016/j.ins.2019.10.062
-
Fattahi Grand (2020) A information-driven approach for supply chain network pattern under doubt with consideration of social concerns. Ann Oper Res 288(1):265–284. https://doi.org/10.1007/s10479-020-03532-9
-
Fu Y, Tian One thousand, Fathollahi-Fard AM, Ahmadi A, Zhang C (2019) Stochastic multi-objective modelling and optimization of an free energy-conscious distributed permutation period shop scheduling trouble with the total tardiness constraint. J Clean Prod 226:515–525. https://doi.org/ten.1016/j.jclepro.2019.04.046
-
Govindan K, Mina H, Alavi B (2020) A decision support system for demand direction in healthcare supply chains because the epidemic outbreaks: a case study of coronavirus disease 2019 (COVID-nineteen). Transportation Research Function E: Logistics and Transportation Review 138:101967. https://doi.org/ten.1016/j.tre.2020.101967
-
Hajiaghaei-Keshteli Chiliad, Fathollahi Fard AM (2019) Sustainable airtight-loop supply concatenation network blueprint with discount supposition. Neural Comput & Applic 31:5343–5377. https://doi.org/10.1007/s00521-018-3369-v
-
Hishamuddin H, Sarker RA, Essam D (2012) A disruption recovery model for a single stage production-inventory system. Eur J Oper Res 222(3):464–473. https://doi.org/10.1016/j.ejor.2012.05.033
-
Ilyas S, Hu Z, Wiwattanakornwong Chiliad (2020) Unleashing the role of meridian management and government back up in green supply chain management and sustainable development goals. Environ Sci Pollut Res 27:8210–8223. https://doi.org/ten.1007/s11356-019-07268-3
-
Islam MT, Azeem A, Jabir Thousand, Paul A, Paul SK (2020) An inventory model for a three-stage supply chain with random capacities considering disruptions and supplier reliability. Ann Oper Res. https://doi.org/10.1007/s10479-020-03639-z
-
Ivanov D (2019) Disruption tails and revival policies: a simulation analysis of supply chain blueprint and product-ordering systems in the recovery and mail service-disruption periods. Comput Ind Eng 127:558–570. https://doi.org/10.1016/j.cie.2018.10.043
-
Ivanov D (2020) Predicting the impacts of epidemic outbreaks on global supply bondage: a simulation-based analysis on the coronavirus outbreak (COVID-19/SARS-CoV-2) example. Transportation Research Part East: Logistics and Transportation Review 136:101922. https://doi.org/10.1016/j.tre.2020.101922
-
Ivanov D, Mason SJ, Hartl R (2016) Supply concatenation dynamics, control and disruption management. Int J Prod Res 54(1):1–7. https://doi.org/10.1080/00207543.2015.1114186
-
Jabbarzadeh A, Fahimnia B, Sabouhi F (2018) Resilient and sustainable supply chain pattern: sustainability analysis under disruption risks. Int J Prod Res 56(17):5945–5968. https://doi.org/10.1080/00207543.2018.1461950
-
Karampour MM, Hajiaghaei-Keshteli M, Fathollahi-Fard AM, Tian Chiliad (2020) Metaheuristics for a bi-objective greenish vendor managed inventory problem in a two-echelon supply chain network. Scientia Iranica. https://doi.org/ten.24200/sci.2020.53420.3228
-
Karmaker CL, Ahmed T, Ahmed S, Ali SM, Moktadir MA, Kabir Thousand (2020) Improving supply chain sustainability in the context of COVID-nineteen pandemic in an emerging economy: exploring drivers using an integrated model. Sustain Prod Consum 26:411–427. https://doi.org/10.1016/j.spc.2020.09.019
-
Kleindorfer PR, Saad GH (2009) Managing disruption risks in supply chains. Prod Oper Manag 14(1):53–68. https://doi.org/10.1111/j.1937-5956.2005.tb00009.x
-
Kolmogoroff A (1931) Über die analytischen methoden in der wahrscheinlichkeitsrechnung. Math Ann 104(one):415–458. https://doi.org/10.1007/BF01457949
-
Konstantaras I, Skouri One thousand, Lagodimos AG (2019) EOQ with independent endogenous supply disruptions. Omega 83:96–106. https://doi.org/10.1016/j.omega.2018.02.006
-
Kumar A, Moktadir MA, Khan SAR, Garza-Reyes JA, Tyagi M, Kazançoğlu Y (2020) Behavioral factors on the adoption of sustainable supply concatenation practices. Resour Conserv Recycl 158:104818. https://doi.org/10.1016/j.resconrec.2020.104818
-
Lopes de Sousa Jabbour AB, Chiappetta Jabbour CJ, Hingley M, Vilalta-Perdomo EL, Ramsden G, Twigg D (2020) Sustainability of supply bondage in the wake of the coronavirus (COVID-xix/SARS-CoV-two) pandemic: lessons and trends. Mod Supply Concatenation Inquiry and Applications, alee-of-p(ahead-of-print). https://doi.org/10.1108/MSCRA-05-2020-0011
-
Majumdar A, Shaw M, Sinha SK (2020) COVID-19 debunks the myth of socially sustainable supply chain: a case of the habiliment manufacture in South Asian countries. Sustain Prod Consum 24:150–155. https://doi.org/10.1016/j.spc.2020.07.001
-
Malik AI, Sarkar B (2020) Disruption management in a constrained multi-production imperfect production system. J Manuf Syst 56:227–240. https://doi.org/10.1016/j.jmsy.2020.05.015
-
Mehranfar N, Hajiaghaei-Keshteli M, Fathollahi-Fard AM (2019) A novel hybrid whale optimization algorithm to solve a production-distribution network problem considering carbon emissions. Int J Eng 32:1781–1789. https://doi.org/10.5829/ije.2019.32.12c.11
-
Mehrbakhsh S, Ghezavati V (2020) Mathematical modeling for dark-green supply chain considering product recovery chapters and uncertainty for demand. Environ Sci Pollut Res 27:44378–44395. https://doi.org/10.1007/s11356-020-10331-z
-
Nezhadroshan AM, Fathollahi-Fard AM, Hajiaghaei-Keshteli Yard (2020) A scenario-based possibilistic-stochastic programming approach to address resilient humanitarian logistics because travel time and resilience levels of facilities. International Journal of Systems Science: Operations and Logistics. https://doi.org/x.1080/23302674.2020.1769766
-
Nguyen H, Sharkey TC, Mitchell JE, Wallace WA (2020) Optimizing the recovery of disrupted single-sourced multi-echelon assembly supply chain networks. IISE Trans 52:703–720. https://doi.org/10.1080/24725854.2019.1670372
-
Nujoom R, Mohammed A, Wang Q (2018) A sustainable manufacturing system design: a fuzzy multi-objective optimization model. Environ Sci Pollut Res 25:24535–24547. https://doi.org/ten.1007/s11356-017-9787-six
-
Pal B, Sana SS, Chaudhuri Grand (2014) A multi-echelon production-inventory system with supply disruption. J Manuf Syst 33(2):262–276. https://doi.org/10.1016/j.jmsy.2013.12.010
-
Parlar M, Perry D (1995) Assay of a (Q, r, T) inventory policy with deterministic and random yields when future supply is uncertain. Eur J Oper Res 84(2):431–443. https://doi.org/10.1016/0377-2217(93)E1075-E
-
Paul SK, Chowdhury P (2020a) A product recovery programme in manufacturing supply chains for a loftier-demand particular during COVID-19. International Journal of Physical Distribution & Logistics Management ahead-of-impress. https://doi.org/10.1108/IJPDLM-04-2020-0127
-
Paul SK, Chowdhury P (2020b) Strategies for managing the impacts of disruptions during COVID-nineteen: an case of toilet newspaper. Glob J Flex Syst Manag 21:283–293. https://doi.org/10.1007/s40171-020-00248-4
-
Paul SK, Sarker R, Essam D (2015) Managing disruption in an imperfect production-inventory organisation. Comput Ind Eng 84:101–112. https://doi.org/ten.1016/j.cie.2014.09.013
-
Paul SK, Sarker R, Essam D (2017) A quantitative model for disruption mitigation in a supply chain. Eur J Oper Res 257(3):881–895. https://doi.org/10.1016/j.ejor.2016.08.035
-
Paul SK, Sarker R, Essam D (2018) A reactive mitigation arroyo for managing supply disruption in a iii-tier supply chain. J Intell Manuf 29(7):1581–1597. https://doi.org/ten.1007/s10845-016-1200-7
-
Pavlov A, Ivanov D, Dolgui A, Sokolov B (2018) Hybrid fuzzy-probabilistic approach to supply concatenation resilience assessment. IEEE Trans Eng Manag 65(ii):303–315. https://doi.org/10.1109/TEM.2017.2773574
-
Rahman MH, Rifat M, Azeem A, Ali SM (2018) A quantitative model for disruptions mitigation in a supply chain because random capacities and disruptions at supplier and retailer. International Journal of Management Science and Engineering Management:1–9. https://doi.org/10.1080/17509653.2018.1436009
-
Revilla East, Saenz MJ (2017) The bear on of take a chance management on the frequency of supply chain disruptions. Int J Oper Prod Manag 37(v):557–576. https://doi.org/10.1108/IJOPM-03-2016-0129
-
Ross SM (1995) 'Schotastic processes' Wiley; 2d edition, ISBN-13 : 978–0471120629
-
Rowan NJ, Galanakis CM (2020) Unlocking challenges and opportunities presented by COVID-19 pandemic for cantankerous-cut disruption in agri-food and green deal innovations: Quo Vadis? Sci Full Environ 748:141362. https://doi.org/10.1016/j.scitotenv.2020.141362
-
Sahebjamnia North, Fathollahi-Fard AM, Hajiaghaei-Keshteli Thousand (2018) Sustainable tire closed-loop supply concatenation network design: hybrid metaheuristic algorithms for big-scale networks. J Clean Prod 196:273–296. https://doi.org/10.1016/j.jclepro.2018.05.245
-
Sarkar B (2012) An inventory model with reliability in an imperfect product process. Appl Math Comput 218(ix):4881–4891. https://doi.org/ten.1016/j.amc.2011.ten.053
-
Sarkar B, Majumder A, Sarkar K, Koli Dey B, Roy G (2017) Two-echelon supply chain model with manufacturing quality improvement and setup cost reduction. Journal of Industrial & Management Optimization 13(2):1085–1104. https://doi.org/x.3934/jimo.2016063
-
Sawik T (2019) Two-period vs. multi-period model for supply chain disruption management. Int J Prod Res 57(14):4502–4518. https://doi.org/x.1080/00207543.2018.1504246
-
Schmitt AJ, Singh Thou (2012) A quantitative assay of disruption risk in a multi-echelon supply concatenation. Int J Prod Econ 139(i):22–32. https://doi.org/ten.1016/j.ijpe.2012.01.004
-
Shokrani A, Loukaides EG, Elias Due east, Lunt AJG (2020) Exploration of alternative supply chains and distributed manufacturing in response to COVID-19; a example study of medical face shields. Mater Des 192:108749. https://doi.org/10.1016/j.matdes.2020.108749
-
Snyder LV, Atan Z, Peng P, Rong Y, Schmitt AJ, Sinsoysal B (2016) OR/MS models for supply concatenation disruptions: a review. IIE Trans 48(ii):89–109. https://doi.org/10.1080/0740817X.2015.1067735
-
Taqi HMM, Ahmed HN, Paul Southward, Garshasbi Chiliad, Ali SM, Kabir G, Paul SK (2020) Strategies to manage the impacts of the COVID-19 pandemic in the supply chain: implications for improving economic and social sustainability. Sustain 12:1–25. https://doi.org/ten.3390/su12229483
-
Tian G, Hao N, Zhou Grand, Pedrycz West, Zhang C, Ma F, Li Z (2019a) Fuzzy grey choquet integral for evaluation of multicriteria decision making problems with interactive and qualitative indices. IEEE Transactions on Systems, Man, and Cybernetics: Systems:1–14. https://doi.org/x.1109/TSMC.2019.2906635
-
Tian G, Liu X, Zhang K, Yang Y, Zhang H, Lin Y, Li Z (2019b) Pick of accept-back pattern of vehicle reverse logistics in China via Grey-DEMATEL and fuzzy-VIKOR combined method. J Clean Prod 220:1088–1100
-
Tripathy PK, Tripathy P, Pattnaik M (2011) A fuzzy EOQ model with reliability and need-dependent unit of measurement toll. Int. J. Contemp. Math, Sciences
-
Tumpa TJ, Ali SM, Rahman MH, Paul SK, Chowdhury P, Rehman Khan SA (2019) Barriers to greenish supply chain management: an emerging economy context. Journal of Cleaner Production 236:117617. commodity. https://doi.org/10.1016/j.jclepro.2019.117617
-
UNCTAD Report (2020) https://unctad.org/en/pages/newsdetails.aspx?OriginalVersionID=2315. Accessed on July 04, 2020
-
World Trade Organization (WTO) (2020) Trade set to plunge equally COVID-19 pandemic upends global economy. Press Release 8 Apr 2020. https://www.wto.org/english language/news_e/pres20_e/pr855_e.htm
-
Xu 10, Guo WG, Rodgers MD (2020) A real-time determination support framework to mitigate degradation in perishable supply chains. Comput Ind Eng 150:106905. https://doi.org/x.1016/j.cie.2020.106905
-
Yoon J, Talluri S, Rosales C (2020) Procurement decisions and information sharing under multi-tier disruption adventure in a supply chain. Int J Prod Res 58(5):1362–1383. https://doi.org/x.1080/00207543.2019.1634296
Acknowledgments
This research was conducted at Bangladesh University of Engineering science and Technology (BUET). The authors admit the supports received from the Section of Industrial and Product Engineering (IPE) of BUET for carrying out this inquiry successfully. The authors too acknowledge the supports of Vadim Five. Ponkratov of Financial University under the Government of the Russian federation to revise this article.
Writer information
Affiliations
Contributions
Kazi Safowan Shahed: Conceptualization, Methodology, Software, Formal analysis, Investigation, Data Curation, Writing – original draft, Dr. Abdullahil Azeem: Conceptualization, Resource, Writing – review and editing, Supervision, Dr. Syed Mithun Ali: Conceptualization, Resources, Writing – review and editing, Physician. Abdul Moktadir: Resources, Visualization, Writing – review and editing.
Corresponding author
Ethics declarations
Competing interests
The authors declare that they have no competing interests.
Ethical approval
Non applicative.
Consent to participate
Not applicative.
Consent for publication
All authors have read the final version of the article and agreed to publish it to Environmental Science and Pollution Inquiry.
Additional information
Publisher'due south notation
Springer Nature remains neutral with regard to jurisdictional claims in published maps and institutional affiliations.
Responsible editor: Lotfi Aleya
Appendices
Notations used in the study
In this study, the following notations are used.
Transient probability calculation
Let Ten(t) = (Xij (t)), t ≥ 0, i,j = 0, ane, 2, iii be the 4 × 4 matrix of transition functions for the CTMC. We tin use the Kolmogorov forward equations (Kolmogoroff 1931), which is a system of ordinary differential equations, to derive the transient probabilities from the matrix. A generic form of the equation is given below:
$$ X\hbox{'}{}_{\mathrm{ij}}(t)=-\upvarphi \left(\mathrm{j}\right){X}_{\mathrm{ij}}(t)+{\Sigma}_{\mathrm{k}\ne \mathrm{j}}{X}_{\mathrm{iy}}(t)\upvarphi \left(chiliad,j\right) $$
(three)
Here, the k represents an intermediate state in between the state i and j. The rate out of any state is denoted past φ. In the same manner, other differential equations can be derived. Equally in that location are 4 states, at that place are 16 Kolmogorov equations. They tin can be put in a matrix differential class, which is more convenient. The matrix is given below:
$$ \boldsymbol{X}\hbox{'}\left(\boldsymbol{t}\right)=\boldsymbol{X}\left(\boldsymbol{t}\right)\boldsymbol{Q} $$
(4)
where Q is \( \left[\begin{array}{cccc}-\left(\lambda +\alpha \right)& \alpha & \lambda & 0\\ {}\beta & -\left(\lambda +\beta \right)& 0& \lambda \\ {}\mu & 0& -\left(\alpha +\mu \right)& \blastoff \\ {}0& \mu & \beta & -\left(\mu +\beta \right)\stop{array}\correct] \).
Here, Q is the generator matrix of the Markoff chain. The solution for the matrix differential equation can exist defined as Ten (t) = e Qt . Here, e Qt is divers as
$$ {e}^{Qt}={\sum}_0^{\infty}\frac{t^n{Q}^due north}{due north!} $$
(5)
It is the matrix exponent. Now, from the spectral theory of the matrices (Hilderbrand)
$$ \boldsymbol{Q}={\boldsymbol{UHU}}^{-} $$
(6)
where U is the nonsingular matrix formed with the right eigenvectors of Q and H is the diagonal matrix. To find the eigenvectors of Q , we first find the eigenvalues
$$ \boldsymbol{\det}\ \left(\boldsymbol{Q}-\omega \boldsymbol{I}\correct)= 0 $$
(seven)
Solving Eq. A5 gives ω 0 = 0, ω one = − (λ + μ), ω 2 = − (α + β), and ω 3 = − (λ + μ + α + β).
The eigenvectors can exist determined by using the eigenvalues to a higher place, and the matrix U is formed as follows:
$$ U=\left[\begin{array}{cccc}one& i& 1& 1\\ {}1& 1& -\beta /\alpha & -\beta /\alpha \\ {}i& -\mu /\lambda & ane& -\mu /\lambda \\ {}1& -\mu /\lambda & -\beta /\alpha & \mu \beta /\lambda \alpha \stop{array}\correct] $$
(8)
$$ \mathrm{If}\ \boldsymbol{Q}={\boldsymbol{UHU}}^{-\boldsymbol{1}},\mathrm{and then}\ {\mathbf{Q}}^{\mathbf{n}}=\left({\mathbf{U}\mathbf{H}}^{\mathbf{n}}{\mathbf{U}}^{-\boldsymbol{ane}}\correct) $$
(9)
Therefore, the final equation for determining the transient probability tin be obtained by substituting the value Q :
$$ \boldsymbol{Ten}\left(\boldsymbol{t}\right)={\displaystyle \begin{array}{c}{\sum}_{n=0}^{\infty}\frac{\left(\boldsymbol{U}{\boldsymbol{H}}^{\boldsymbol{n}}{\boldsymbol{U}}^{-\mathbf{i}}\correct)}{\boldsymbol{n}!}\\ {}=\boldsymbol{UA}\left(\boldsymbol{t}\right)\boldsymbol{U}-\mathbf{1}\ \terminate{assortment}} $$
(ten)
where
$$ Y(t)=\left[\brainstorm{array}{cccc}{e}^{\omega_1t}& 0& 0& 0\\ {}0& {e}^{\omega_1t}& 0& 0\\ {}0& 0& {e}^{\omega_2t}& 0\\ {}0& 0& 0& {e}^{\omega_3t}\end{array}\right] $$
(xi)
Consumption of the order quantity received in land 0 follows the Erlang distribution. The Y 11 will exist derived from the following equation when the received quantity is E (q 0) in state 0:
$$ \boldsymbol{Y}\mathbf{11}={\displaystyle \begin{array}{c}\frac{\gamma }{\Gamma \mathrm{East}\left(\mathrm{q}\right)}{\int}_0^{\infty}\left[{e}^{-\left(\lambda +\mu \right)x}\right]{\left(\gamma ten\right)}^{\mathrm{E}\left(q-1\right)}{e}^{-\gamma 10} dx\\ {}={\left(\frac{\gamma }{\gamma +\lambda +\mu}\correct)}^{E(q)}\finish{array}} $$
(12)
Similarly,
$$ \boldsymbol{Y}\mathbf{22}={\left(\frac{\gamma }{\gamma +\alpha +\beta}\right)}^{East(q)} $$
(13)
And
$$ \boldsymbol{Y}\mathbf{33}={\left(\frac{\gamma }{\gamma +\lambda +\mu +\alpha +\beta}\right)}^{Eastward(q)} $$
(14)
Therefore, the transition probability from land 0 to the other three states tin be calculated from the post-obit matrix.
$$ Y(t)=\left[\begin{assortment}{cccc}one& 0& 0& 0\\ {}0& {\left(\frac{\gamma }{\gamma +\lambda +\mu}\right)}^{Eastward(q)}& 0& 0\\ {}0& 0& {\left(\frac{\gamma }{\gamma +\alpha +\beta}\correct)}^{East(q)}& 0\\ {}0& 0& 0& {\left(\frac{\gamma }{\gamma +\lambda +\mu +\alpha +\beta}\right)}^{E(q)}\end{array}\right] $$
(15)
The value of transition probabilities tin can be generated by using the eigenvector matrix(U) and its inverse(U −1 ) of the generator matrix Q. Based on the quantity received, which volition be consumed, the matrix Y(t) can be one of the three matrices as derived. This received order quantities are too state-dependent.
Cycle profit calculation
Profit is defined as the difference between total revenues and total costs. Hither, for a production cycle, we considered the toll components as property price (for raw textile and finished product), ordering cost, setup cost, purchasing cost, inspection cost (for raw fabric and finished production), rejection cost (for raw material and finished production), production cost, and cost of involvement and depreciation. Now, orders tin be placed to supplier for raw material in example of country 0 only when both the supplier and retailer are available. For other states, the different price is incurred.
Total cost incurred per production bicycle = holding cost + ordering cost + setup toll + purchasing cost + inspection cost + rejection cost + production toll + price of involvement and depreciation
Now, the expressions of different price components are given below:
-
Property cost =\( \frac{h_sE(q)}{\gamma}\times \frac{E(q)+2r}{2{n}_s}+\frac{h_mE(q)}{\gamma}\times E(q)\times {north}_m=\frac{h_sE\left({q}^2\right)}{2\gamma {n}_s}+\frac{h_sE(q)r}{\gamma {due north}_s}+\frac{h_mE\left({q}^2\correct){n}_m}{\gamma } \)
-
Purchasing price =\( P\times \frac{E(q)}{n_s} \)
-
Inspection cost =\( P\times {e}_1\times \frac{E(q)}{n_s}+P\times {e}_2\times E(q) \)
-
Rejection cost =\( {C}_1\times East(q)\times \frac{\left(1-{n}_s\right)}{n_s}+{C}_2\times East(q)\times \left(1-{n}_m\right) \)
-
Production toll =Eastward(q) ×P p
-
Toll of involvement and depreciation =a(South)−b (n m ) c
$$ \mathrm{Thus},\mathrm{the}\ \mathrm{total}\ \mathrm{cost}\ \mathrm{incurred}\ \mathrm{per}\ \mathrm{production}\ \mathrm{bike}=\frac{h_sE\left({q}^2\right)}{2\gamma {n}_s}+\frac{h_sE(q)r}{\gamma {n}_s}+\frac{h_mE\left({q}^two\right){north}_m}{\gamma }+thou+S+P\times \frac{E(q)}{n_s}+P\times {e}_1\times \frac{E(q)}{n_s}+P\times {e}_2\times E(q)+{C}_1\times Eastward(q)\times \frac{\left(one-{northward}_s\right)}{n_s}+{C}_2\times E(q)\times \left(1-{due north}_m\right)+Eastward(q)\times {P}_p+a{(S)}^{-b}{\left({due north}_m\correct)}^c $$
(xvi)
where
\( Eastward(q)=\frac{1}{\psi}\times \left(1-{e}^{-\psi q}\right) \) and \( Eastward(q2)=\frac{2}{\psi^2}\times \left\{1-\left(1+\psi q\right){e}^{-\psi q}\right\}. \)
At present, revenue generated per cycle = selling cost of acceptable units + selling price of faulty units
$$ \mathrm{Therefore},\mathrm{revenue}\ \mathrm{generated}\ \mathrm{per}\ \mathrm{wheel}=P\times {one thousand}_1\times E(q)\times {n}_m+P\times {m}_1\times E(q)\times \left(ane-{n}_m\right) $$
(17)
Consequently,
$$ \boldsymbol{AP}\left(E(q),r,{n}_s,{n}_m\correct)=P\times {thousand}_1\times East(q)\times {n}_m+P\times {m}_1\times East(q)\times \left(ane-{due north}_m\correct)-\frac{h_sE\left({q}^2\right)}{2\gamma {n}_s}-\frac{h_sE(q)r}{\gamma {n}_s}-\frac{h_mE\left({q}^2\right){northward}_m}{\gamma }-k-Southward-P\times \frac{E(q)}{n_s}-P\times {eastward}_1\times \frac{East(q)}{n_s}-P\times {e}_2\times E(q)-{C}_1\times E(q)\times \frac{\left(1-{northward}_s\correct)}{n_s}-{C}_2\times Due east(q)\times \left(1-{due north}_m\correct)-E(q)\times {P}_p-a{(Southward)}^{-b}{\left({due north}_m\correct)}^c $$
(18)
Transition price, C i0 , is defined as the cost of reaching state 0 starting from country i. Once again, other states can be reached before reaching country 0. Subsequently, values of those elements (C 10, C twenty, C 30) are evaluated.
$$ {C}_{00}={X}_{00}\left(Due east(q)\correct)A\left(E(q),r,{n}_{s,}\ {n}_m\right)+{\sum}_{j=ane}^3{P}_{ij}\left(E(q)\right)\left[\ {C}_{j0}\right];i=0,1,2 $$
(19)
The above equation signifies that subsequently receiving the expected quantity from the supplier, the new inventory level will be E(q)+r. Later on the East(q) unit is finished, the manufacturer volition notice him/her either in state 0, 1, 2, or iii with respective probability of X 00 (E(q)), X 01 (Eastward(q)), X 02 (E(q)), and X 03 (E(q)).
So, nosotros detect
$$ {C}_{0 0}={Ten}_{0 0}\ {A}_0+{X}_{0 i}{C}_{10}+{X}_{0 2}{C}_{20}+{10}_{0 3}{C}_{30} $$
(twenty)
For C 10, we can write
$$ {C}_{10}={Ten}_{10}C\bar{\mkern6mu}\bar{\mkern6mu}{}_{ten}+{X}_{11}{C}_{ten}+{10}_{12}{C}_{20}+{10}_{13}{C}_{xxx} $$
(21)
For C 20 , we tin can write
$$ {C}_{20}={X}_{20}C\bar{\mkern6mu}\bar{\mkern6mu}{}_{20}+{X}_{21}{C}_{ten}+{10}_{22}{C}_{20}+{X}_{23}{C}_{30} $$
(22)
But C 30 has a different expression.
$$ {C}_{30}=\left(C\bar{\mkern6mu}\bar{\mkern6mu}+{C}_{10}\correct){\rho}_1+\left(C\bar{\mkern6mu}\bar{\mkern6mu}+{C}_{ii 0}\right){\rho}_2=C\bar{\mkern6mu}\bar{\mkern6mu}+{C}_{ten}{\rho}_1+{C}_{2 0}{\rho}_2 $$
(23)
where
$$ {\rho}_1=\frac{\mu }{\mu +\beta}\kern0.5em \mathrm{and}\ {\rho}_2=\frac{\beta }{\mu +\beta } $$
Then, we evaluate the value of C̅, C̅ ten, and C̅ 20 .
$$ \mathrm{Therefore},{C}_{0 0}={Ten}_{0 0}{A}_0+{10}_{0 one}{\sigma}_1+{X}_{0 2}{\sigma}_2+{X}_{0 3}\ \left(C\bar{\mkern6mu}\bar{\mkern6mu}+{\rho}_1{\sigma}_1+{\rho}_2{\sigma}_2\right) $$
(24)
where [σ 1 σ 2 ]' = [C ten C xx ]'.
Cycle length adding
Now, we define the length of cycle T 00 . From the inquiry of Ahmed et al. (2017), we can define T i0 =E (fourth dimension at the offset of the next cycle from the time when inventory drops to r at land i = 0, 1, 2, iii and q units are ordered in case of state 0).
Then,
$$ {T}_{i0}={X}_{i0}\left(East\left({q}_i\right)\right)\times \frac{E\left({q}_i\right)}{\gamma }+{\sum}_{j=1}^3\ {X}_{ij}\left(East\left({q}_i\right)\right)\left[\frac{Eastward\left({q}_i\right)}{\gamma }+{T}_{j0}\right];i=0,1,ii $$
(25)
Cycle length T 00 can exist derived from the equation above:
$$ {T}_{00}={X}_{00}\left(Eastward\left({q}_i\right)\correct)\times \frac{East\left({q}_0\right)}{\gamma }+{\sum}_{j=1}^3\ {X}_{0j}\left(E\left({q}_0\right)\right)\left[\frac{Due east\left({q}_0\right)}{\gamma }+{T}_{j0}\right] $$
(26)
The above equation signifies that after receiving the expected quantity from the supplier, the new inventory level will be E(q)+r. After the E(q) unit is finished, the manufacturer will observe him either in state 0, 1, 2, or 3 with respective probability of X 00 (E(q)), X 01 (Due east(q)), X 02 (E(q)), and X 03 (E(q)).
Here,
$$ {T}_{00}=\frac{Due east(q)}{\gamma }+{Ten}_{01}{T}_{10}+{X}_{02}{T}_{20}+{Ten}_{03}{T}_{30} $$
(27)
For T 10, nosotros tin write
$$ {T}_{10}={10}_{10}{\overline{T}}_{10}+{X}_{eleven}{T}_{10}+{X}_{12}{T}_{twenty}+{10}_{xiii}{T}_{thirty} $$
(28)
For T 20, we tin write
$$ {T}_{20}={Ten}_{20}{\overline{T}}_{twenty}+{X}_{21}{T}_{10}+{Ten}_{22}{T}_{xx}+{X}_{23}{T}_{30} $$
(29)
And the equation of T xxx is obtained equally follows:
$$ {T}_{thirty}=\overline{T}+\frac{\mu }{\delta }{T}_{ten}+\frac{\beta }{\delta }{T}_{20} $$
(thirty)
where δ = μ + β.
$$ \mathrm{So},{T}_{00}=\frac{Eastward(q)}{\gamma }+{X}_{01}{T}_{x}+{X}_{02}{T}_{20}+{10}_{03}\left(\overline{T}+{\chi}_1{\rho}_1+{\chi}_2{\rho}_2\right) $$
(31)
where [χ 1 χ 2 ]' = [T ten T 20]'
Cycle acquirement calculation
At present, we ascertain the revenue generated in a cycle, R 00. Let us ascertain R i0 =E (revenue to the commencement of the next bike from the time when inventory drops to r at state i = 0, ane, two, 3 and q units are ordered in case of land 0).
Then,
$$ {R}_{i0}={X}_{i0}\left(E\left({q}_i\right)\right)\times {Z}_{i0}\left(E\left({q}_i\right),{n}_m\right)+{\sum}_{j=1}^iii\ {Ten}_{ij}\left(E\left({q}_i\correct)\right){Z}_{j0}\left(East\left({q}_i\right),{north}_m\right);i=0,1,2 $$
(32)
From this equation, R 00 can be defined as
$$ {R}_{00}={10}_{00}\left(Due east\left({q}_i\right)\right)\times {Z}_{00}+{\sum}_{j=1}^3\ {X}_{0j}\left(E\left({q}_0\right)\right){Z}_{i0} $$
(33)
Here, acquirement is generated when country transits from country 0 to country 0.
$$ {R}_{00}=\kern0.5em P\times {m}_1\times E(q)\times {n}_m+P\times {grand}_2\times E(q)\times \left(1-{n}_m\correct) $$
(34)
Rights and permissions
Almost this article
Cite this article
Shahed, M.S., Azeem, A., Ali, S.M. et al. A supply chain disruption risk mitigation model to manage COVID-nineteen pandemic take chances. Environ Sci Pollut Res (2021). https://doi.org/10.1007/s11356-020-12289-four
-
Received:
-
Accustomed:
-
Published:
-
DOI : https://doi.org/10.1007/s11356-020-12289-4
Keywords
- Supply chain disruption
- Supply chain resiliency
- COVID-nineteen
- Genetic algorithm
- Pattern search algorithm
- Inventory policy
- Supply chain mitigation
Source: https://link.springer.com/article/10.1007/s11356-020-12289-4